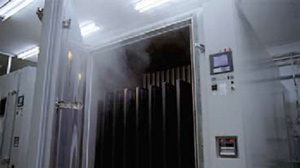
1) Humidity freeze test; 2) High temperature and humidity test |
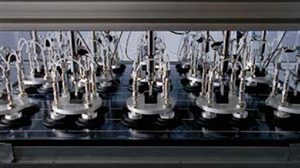
3) Continuous-flow wind tunnel test |
Sharp Corporation has established a new standard*1 for assessing the quality of photovoltaic modules. The standard incorporates criteria stipulated by the VDE Testing and Certification Institute (VDE)*4, a third-party certification institute specializing in electronic equipment safety. Sharp will begin using its new standard to assess crystalline photovoltaic modules released from now on.
Until now, Sharp has been verifying the long-term reliability of photovoltaic modules by complementing the IEC's international quality assessment standards*2 with its own proprietary quality assessment standards. Sharp's verification tests have included accelerated deterioration testing (systematic deterioration of a product under high temperatures and humidity) that utilizes data gathered from the 30-year operation history of a solar panel installation at Tsubosaka Temple in Nara, Japan (installed in 1983). Sharp has also used the PID*5 test and continuous-flow wind tunnel test.
Since Sharp's new standard incorporates a continuous-flow wind tunnel test and a terminal strength test, both stipulated by VDE, it conforms to both IEC standards and the original VDE certification standard. Sharp can thus shorten the verification period by performing tests under one standard instead of several.
Sharp will continue to use strict quality assessment standards as the basis for making high-quality photovoltaic modules that customers can use long term with peace of mind.
- *1 As a standard for assessing Sharp-made crystalline photovoltaic modules.
- *2 Standards stipulated by the IEC (International Electrotechnical Commission), an international standardization organ for electrical and electronic engineering and related fields. 'IEC standards' refers to IEC 61215 (ed. 2) for performance and reliability and IEC 61730-2 (ed. 1) for safety.
- *3 The original VDE certification standard is called the 'VDE Quality Tested' mark for PV modules. Jointly developed with the Fraunhofer Institute for Solar Energy Systems (an internationally leading solar energy research institute) and the solar industry, VDE Quality Tested is a stringent testing and certification program for validating and ensuring consistent production quality for photovoltaic modules.
- *4 The VDE Testing and Certification Institute is a significant part of the VDE Association for Electrical, Electronic and Information Technologies, which is one of the largest technical and scientific associations in Europe with more than 35,000 members. The VDE Institute is an independent institution that is responsible for testing and certifying the safety and performance of electronic devices, components, and systems for the consumer and the general public using the highest standards of quality. Cooperation agreements in more than 50 countries ensure that the inspections of the VDE Institute are internationally recognized. Millions of electrical products worldwide carry VDE certification marks.
- *5 PID (Potential Induced Degradation) is the loss of electrical output due to high temperatures, humidity, and system voltage.
Correlation between Quality Assessment Standards (Overview of Main Criteria)
IEC standards |
1) Humidity freeze test
Verify that there are no problems due to condensation or frost from the day-to-night temperature change.
• Conditions: Temperature of -40℃ to 85℃ (85% humidity), 10 temperature and humidity changes per day. |
2) High temperature and humidity test Verify that there is no loss of electrical output due to material degradation from high temperature and humidity.
• Conditions: Temperature of 85℃, humidity of 85%, for 1,000 hours. |

Sharp's
conventional
standards |
1) Humidity freeze test
More repetition (approx. 10 times more) than IEC tests. |
2) High temperature and humidity test Longer period (several times longer) than IEC tests. |
3) Continuous-flow wind tunnel test
Verify that there are no problems with the solar cell module after it bends from exposure to high wind.
• Panels are continuously pushed and pulled inside the test machine. |
4) Terminal strength test Verify the strength of terminals (cables) joining individual solar cell modules.
• Continuously place physical pressure on the terminals. |
5) Manufacturing process checkup
Take modules off the production line for testing. Verify the continuity of the quality assessment system. |
|

New Sharp quality assessment standard |
1) Humidity freeze test
More repetition (approx. 10 times more) than IEC tests.
(Continuation of Sharp’s conventional standards.) |
2) High temperature and humidity test Longer period (several times longer) than IEC tests.
(Continuation of Sharp's conventional standards.) |
3) Continuous-flow wind tunnel test
Incorporates the VDE original standard.
(Same impact strength and number of repetitions.) |
4) Terminal strength test Incorporates the VDE original standard.
(Same impact strength and same points of impact.) |
5) Manufacturing process checkup
Incorporates the VDE original standard.
(Adds more tests per year and more periodic spot testing.) |
|